PARAMETER OF EQUIPMENT FUNCTION
1.Designed speed 240m/min
2.Working speed 550pcs/min(Small size)
3.Qualified rate 97%
(The rate is compared with qualified products with gross output products within7.5 hours)
4.Efficiency ≥85%
(The rate is compared real output with principle output within 7.5 hours)
5.Installed capacity 280KW (Including hot melt system)
6.Practical capacity 200KW(Including hot melt system) Breaker Capacity:600A
7.Electric power supply Three-phase & four-wire 380V/50HZ(Ground wire)
8.Electric wire 3×120 mm2+1×50 mm2+1×25 mm2
9.Lowest barometric pressure 8 kg/cm2
10.Air compressor >0.6Mpa, 1.8 m3/min, 22kw(to be reference)
11.Gross weight 70000kg
12.Noise <85dB(A)
13.Machine size 32m×8m×3.5m
14.working space 38m×12m×4m
15.Color Silver (According to order)
16.Range of products Five Sizes ( XXL、XL、L、M、S)
17.Length of products 580mm(XXL)、540mm(XL)、500mm(L)、450mm(M)、390mm(S)
18.Container 4×40HQ+1×20GP
Auto control functions:
1. All electrical parts strictly pass CE standard.
2. Total 7 kinds raw materials using 14 servo motors make the raw materials automatic unwinding, tension control, automatic splicing and changing raw materials without lower the speed.
3. There are total 9 set web guard system to control the different kinds raw materials. The +-1MM accuracy ensures the right precision and less the raw materials width for economic cost.
4. PLC+ touch screen +frequency control system . Adopted operating interface. Press the programmable menu for every operation. Every dates can be easily adjusted, recorded and seek.
4.1 Quantity of Sap and Fluff pulp can be set up on the touch screen
4.2 Touch screen can control the main machine speed, the current speed can be shown on the touch screen.
4.3 The machine will automatic stop if the electrical equipments broken, touch screen will shown the error and save the error records.
4.4 single shift output quantity and total production output quantity can be shown on the screen.
5. Auto checking for raw materials: When any of the raw materials lacking or breaking off, the machine can be shut off automatically at the shortest time to decrease the defective.
6. Auto checking and rejecting for all raw materials spliced part by fiber sensor.(Require the connection of the raw materials to be colored).
7. Auto rejecting spliced and other defective products to increase acceptance rate. The photo sensors auto check the defective parts and feed back the relative signals to the PLC. The PLC calculates the distance between the defective product and rejecting outlet and the defective product goes through the rejecting outlet the blowing hole activates to blow it away.
8. The temperature can be controlled by Mercury conducting ring .Each unit adopted individual digital temperature indicator. Each data is set on requirement to meet different consumption. The real time temperature can be fed back to the PLC and displayed at the interface screen.
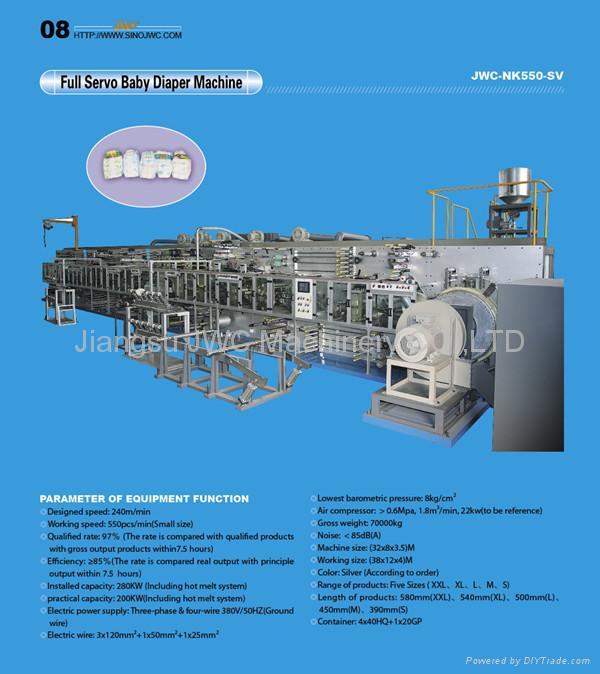